Modifying tooling for custom-made tube profiles

How we make or modify tooling to create new tube shapes and sizes
Timeless make over 250 sizes of oval tube alone.
Most of the sizes across our range of unique profiles have been developed in response to requests for a bespoke size to fit the client’s application. When a new size is required, we achieve this by either modifying our existing tooling or creating new tooling altogether.
Refining the shape of the oval tube
Occasionally a client needs the vertex of the ellipsis (the end points on the major axis) to be more pointed than the more rounded vertex that our rollers form. This was the case with one client, who needed a more pointed ellipsis to fit existing cast parts for their 47x25x1.5mm stainless steel push bar door handle. In this instance we made new hardened steel rollers to form this more pronounced, slightly pointed vertex.
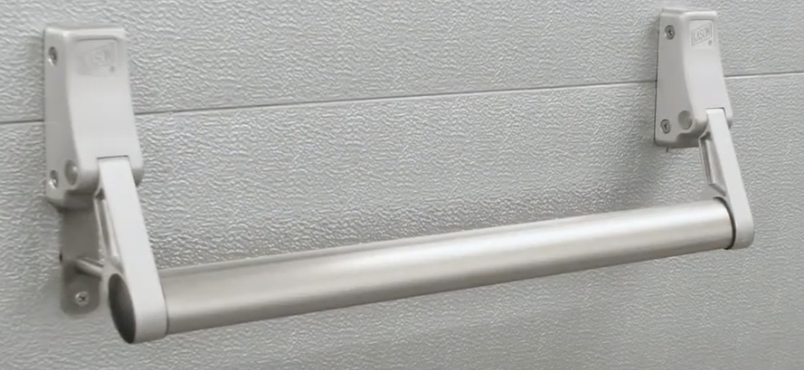
D-shaped press tool - an alternative means of cold-forming
In the case of our smallest D-shaped tube, developed specifically for Osprey Measurements’ IPX sensor, our usual ‘drawing’ method created a surprising effect – the super-slender profile bowed when we tried to form it in long lengths.
We abandoned the drawing method altogether, and instead counteracted this unwanted springiness by creating a tool that applies a compressive force onto smaller cut sections of tube. This alternative pressing method transforms round tube into Osprey’s slimline 20x12.5x1.6mm D-shaped profile.
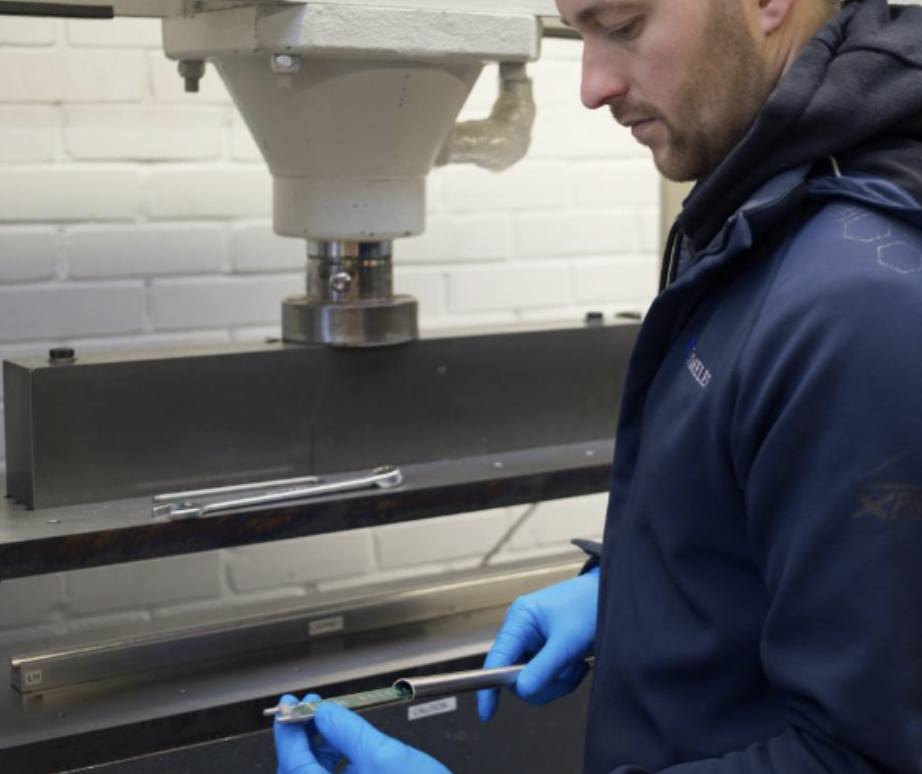
Teardrop tooling to make new shapes
Occasionally a client requests a completely new shape, which will always require new tooling. When investing in new tooling, we often use either aluminium or nylon tooling in forming trials before committing to using the more expensive D2 hardened steel tooling needed for production. This allows us to make any required modifications during these earlier stages of development.

A renowned railings specialist came to Timeless Tube for a bespoke teardrop-shaped railing for their client. The railing was custom-designed for the Thames embankment of a high-end residential development in London’s prestigious Chelsea Waterfront.
Initially aluminium tools were made to prove that the wing-shaped asymmetrical profile was achievable.
Once we were all happy with the teardrop shape, we made the final forming tools from D2 hardened steel. This harder, more substantial tooling allowed us to put greater pressure on the tube during production, creating smoother, flatter sides. We also experimented with various wall thicknesses to see which formed best.
Working with copper to form ‘the hex’
Timeless Tube were tasked with recreating an ornate copper tube design for an iconic shop front in central London. The tube needed to be an exact match of the existing window trim. Making what Timeless refers to as ‘the hex’ was a challenge; especially because it was made from copper, which is a particularly soft metal.
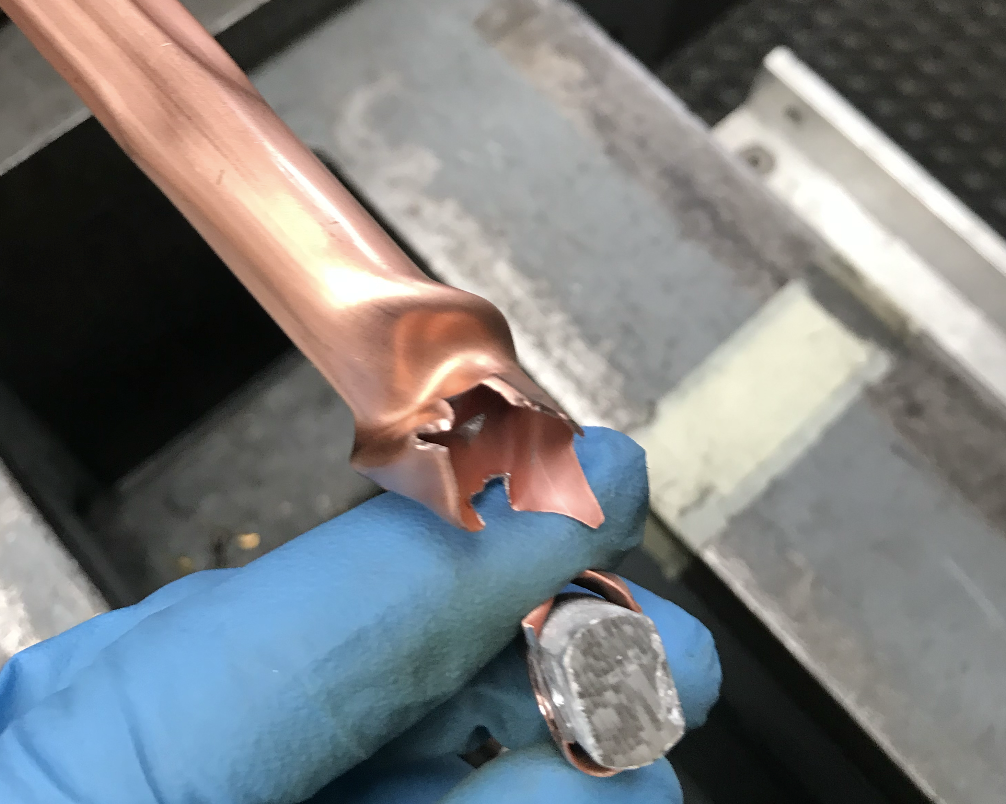
This prolonged development process saw this relatively delicate metal shear and buckle on numerous occasions. We therefore needed to provide internal support for the tube during forming. We trialled wax and resin, eventually finding the support we needed from wood dowel which sat in the centre of the tube during forming.
We finally created a successful match to the original - an intricate design unlike any other profiles that we have formed before.
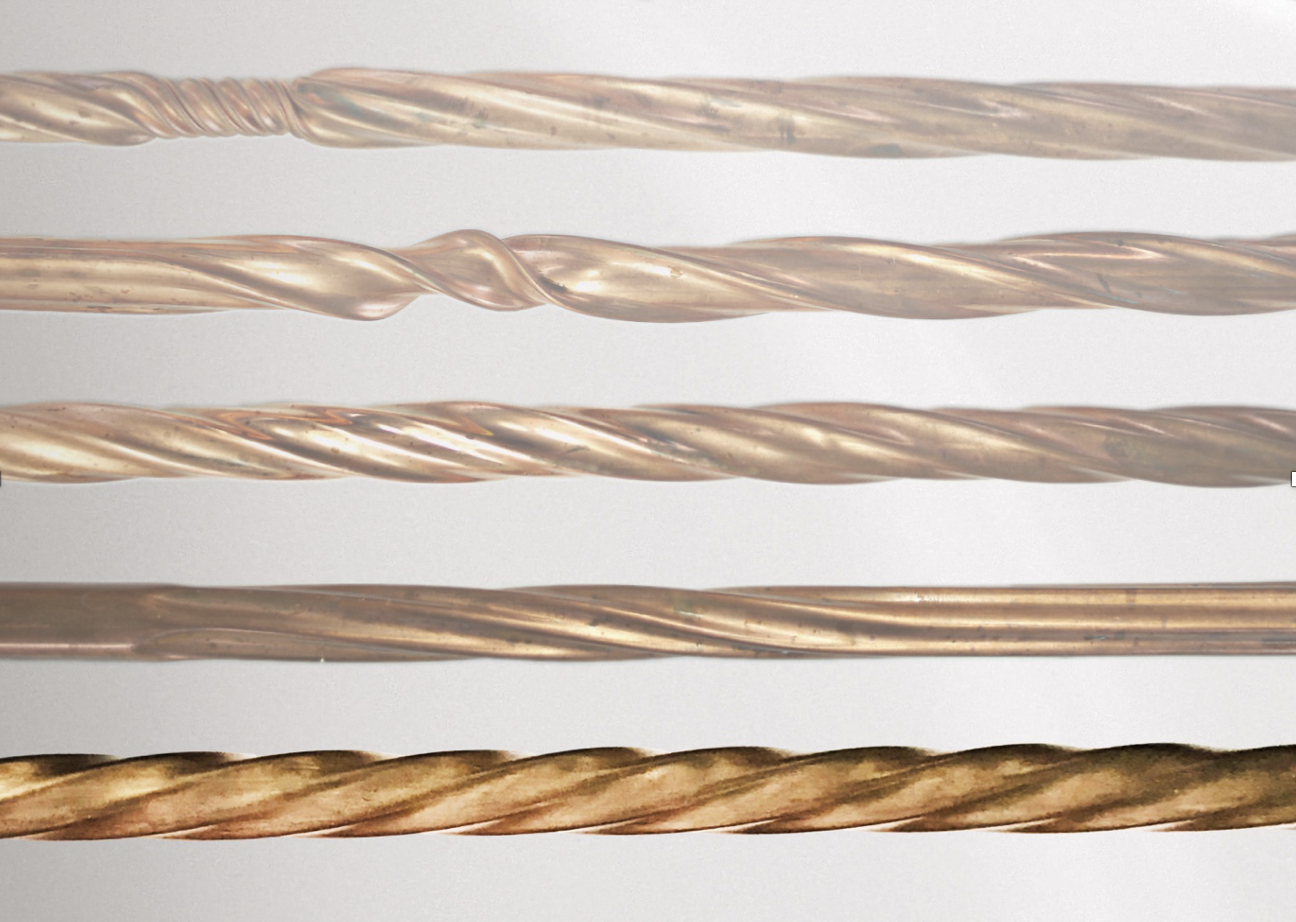
More stories
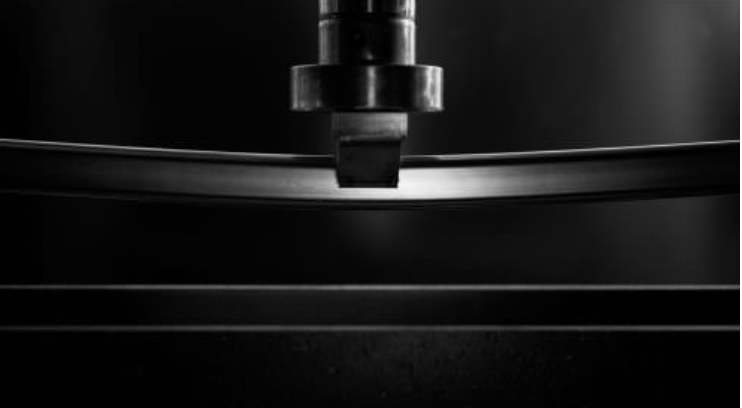
Proving the strength of formed tubes using mechanical bend tests
An exploration into two independent axial load tests on our stainless steel formed profiles, plus a brief look at how we calculate the degree of bends for formed tubes.
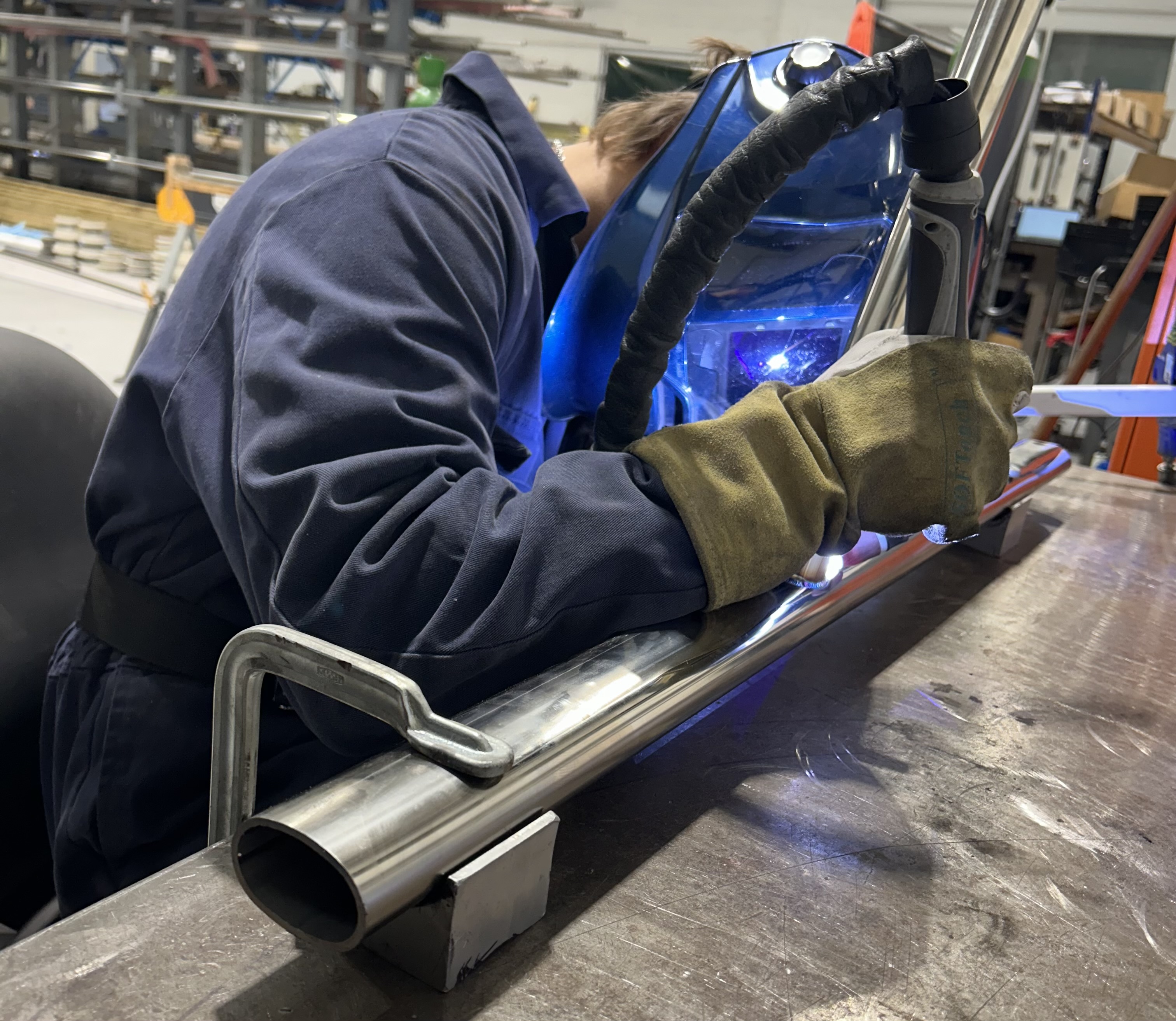
Exhibitors Timeless Tube engineer tube-based showcase for Southern Manufacturing and Electronics trade fair
Visitors to leading trade show for engineers and manufacturers to experience a showcase of innovative tube designs
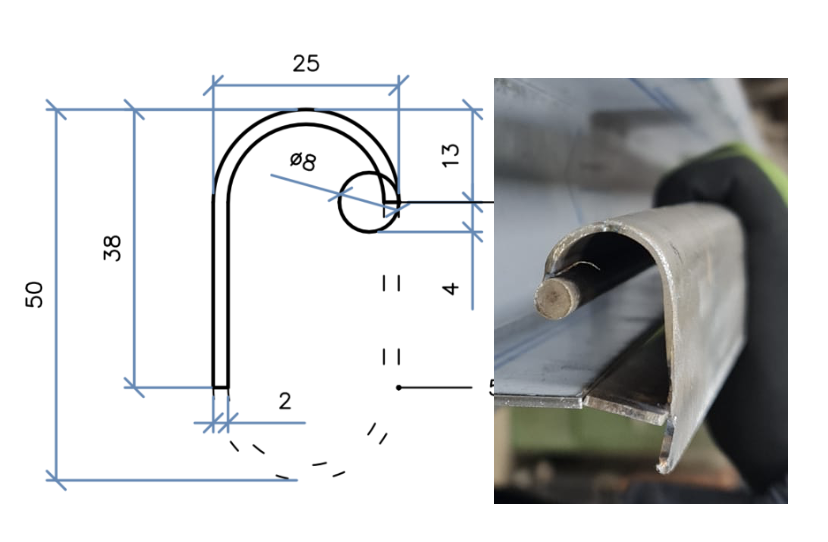
Cut Flat-sided Oval Tube Features in Stunning Recessed Handrail Project
Achieving unique designs often requires embracing trial and error. Timeless had the pleasure of working with pioneering UK-based bespoke steel fabricators Metcalfe on a one-of-a-kind recessed handrail