Tube fabrication specialists leave client feeling 'over the moon'
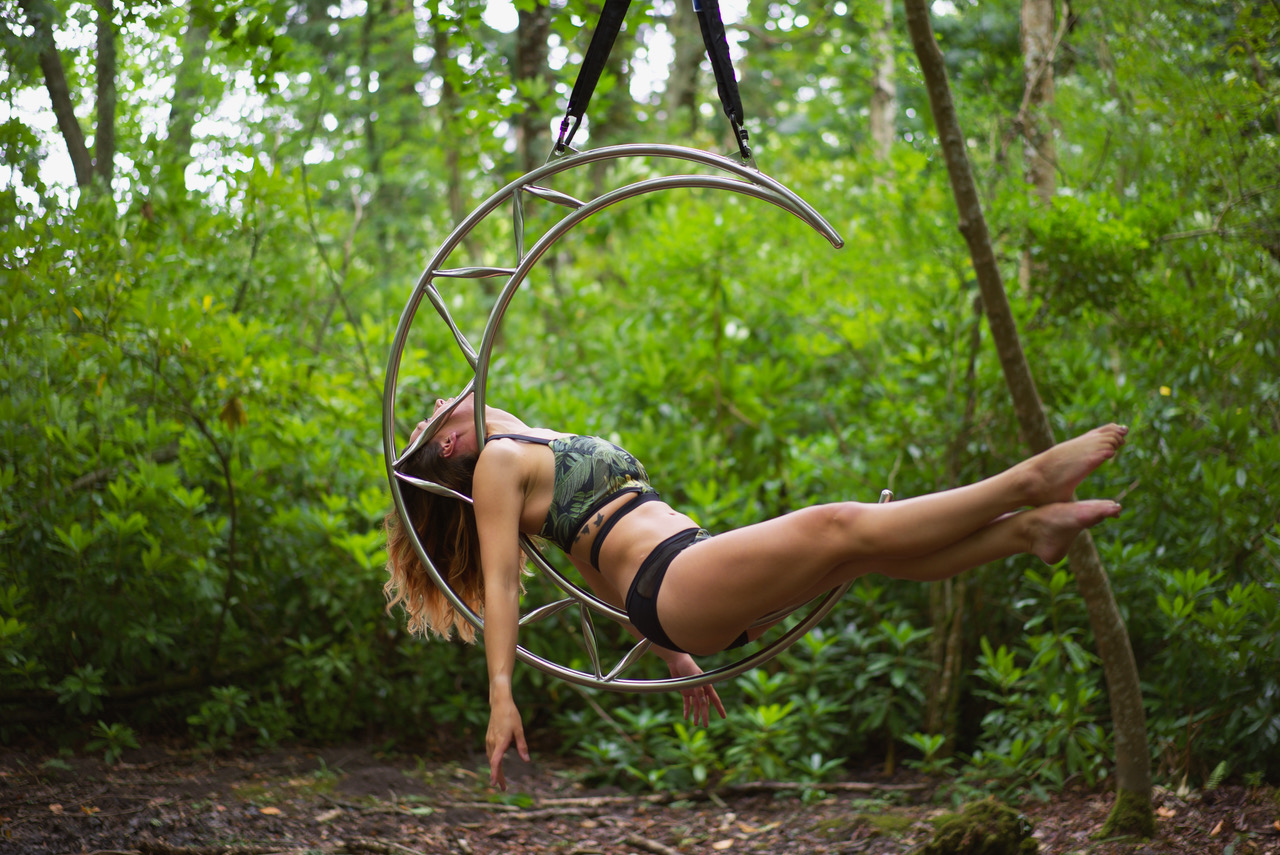
Timeless Tube demonstrate how they are more than just a stainless steel tube supplier with this beautifully fabricated aerialist equipment — Fully fabricated at the Timeless workshop
Timeless MD and Head Engineer Tom McMillan worked closely with British dance and performance-wear designer Fenella Marie to create her artistic vision out of high-quality stainless steel 316L tube.
The moon-inspired tubular apparatus was fully fabricated at the Timeless workshop in Poole, Dorset.
The unique aerialist equipment required several fabrication processes. “This project involved bending, shaping, welding and polishing. The only process that didn’t happen in-house was the post-production weight-testing, which needed to be done offsite by an independent tester” says McMillan.
Design feasibility: working closely with the client to form a solution
Performance wear costume designer Fenella Marie decided to commission the piece for both her own use as an aerialist, as well as for photoshoots. “I wanted to have a really special piece of equipment to use in photoshoots when I showcase the costumes that I design and make. A unique piece of apparatus with WOW factor”.
The aerialist equipment was required to be both beautiful and practical.
Engineer McMillan explains: “We make a lot of bespoke stainless steel handrails here at Timeless, forming stainless steel round tubes into shaped profiles because they are aesthetically and ergonomically superior to round tube. D-shaped tube and oval tube are easier to grip than round tube. They are less prone to slippage – and this is ideal for handrail. However, an aerialist needs to be able to move comfortably around the structure of their apparatus at different angles – whether hanging from the hocks of their knees or in an elbow grip. So for this project, most of the tubing that we used was not actually formed into one of our signature shaped profiles. We needed to use round tube.”
The client was advised to choose stainless steel 316L for the apparatus because 316L is highly durable, with impressive anti-corrosion credentials. This ‘marine-grade’ rust-proof stainless steel is ideal for applications that will be used outdoors and need protecting from the elements.
The tubing was supplied with a mirror polish.
Smaller pieces of stainless steel twisted oval tube sections were welded between the two round tubular crescents, which were used to transform the round tube structure into a special design.
Tube bending
Timeless engineers fed lengths of round tube through a triple roller machine to create two sweeping arcs — the shorter length of tube forming the inside of the moon’s crescent shape.
Typically when Timeless engineers bend tubing, their clients supply drawings that specify the exact radiuses required (and sometimes when the radius is unknown, such as for replacement railings on boat refits, Timeless measure existing railings in order to calculate the radius). However, the process was different with the moon apparatus, which evolved organically, with experimentation at the heart of the making.
“The shorter length of tube had a tighter radius than the longer length, but we worked out the radius by eye.” explains McMillan.
The tube could be fed back through the rolling machine once bent, allowing Tom and his team to make necessary adjustments. This afforded them a level of flexibility that was extremely useful when making this bespoke product. “For this project we used our judgment to create two C-shapes that fitted nicely within one another to form a crescent. Bending round tube is far easier than bending complex geometric profiles such as oval tubing. Round tube has a symmetrical cross-section, so it is very stable and bends in a predictable way.” says McMillan.
Creating twisted oval stainless steel tube
To add interest to the piece, Timeless made 10 smaller pieces of stainless steel twisted oval pieces measuring 23x13x1.5mm. Like the larger round tube structure, these had a bright polish (mirror polish) finish.
Unique to Timeless Tube, these decorative tube twists needed to be ‘ovalised’ before a continuous twist was added. They were then cut into smaller sections of approximately 200mm long (the lengths differed depending upon where they sat within the crescent). “The flourishes that set this performance piece apart are the twisted tube sections that sit within the moon. Placed into a triangular pattern, the twists form the points of a star. These contoured pieces refract the light beautifully.” adds McMillan.
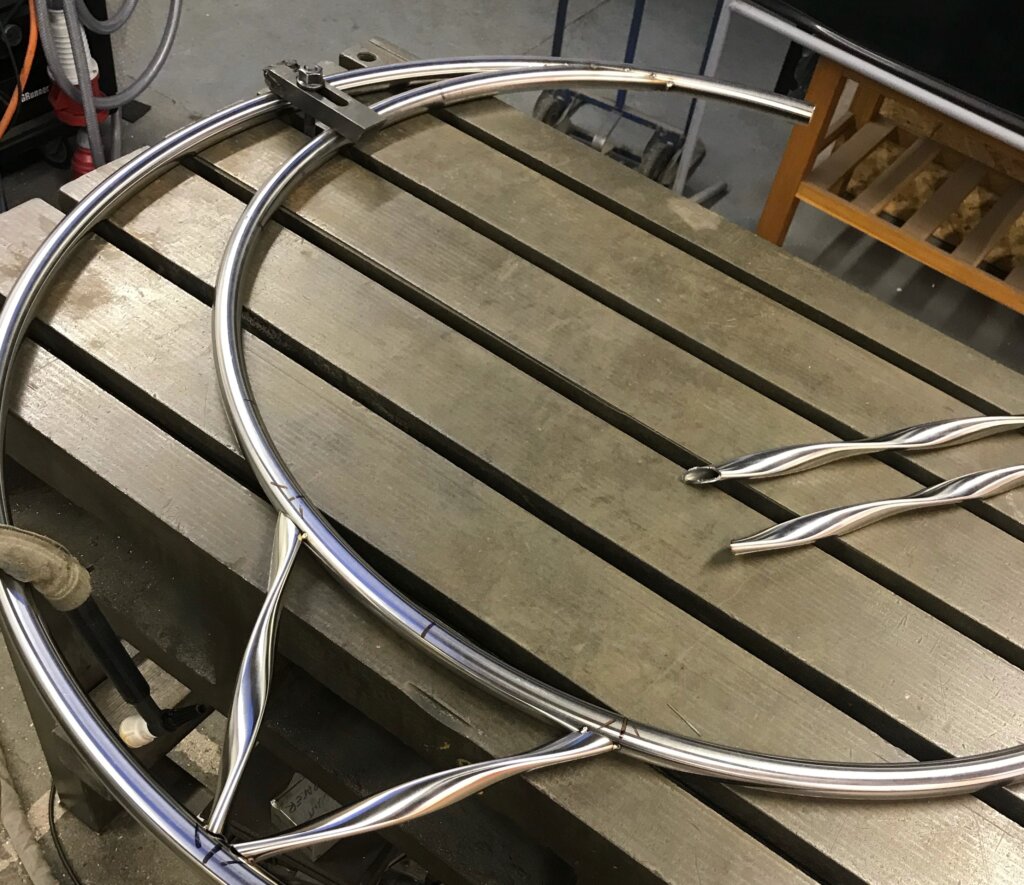
Tig-welding stainless steel tube
The two arcs needed to be welded together before the smaller twists were welded into the crescent.
Timeless used TIG-welding as opposed to MIG-welding, as the one-off piece required an intricate, tidy finish with high-quality joins. TIG-welding is typically Timeless’s preferred method of welding for decorative or precision work as the welds are cleaner. Unlike MIG-welding, there is no need to aggressively grind off unwanted welding material – this makes for stronger joins, too.
The ends of the arcs were cut by hand using an angle grinder before they were clamped, tacked then fully welded together.
The process was slightly different with the smaller twists. Before these were welded to the main structure, Timeless worked with designer Fenella Marie to experiment with the placement of each ornamental tube twist. This was to see not only what looked best but where hands would most likely be placed by aerialist performers.
Before these ornamental tube twists were welded in, they were hand-scalloped with a belt sander. This linishing process created a neat mating joint so there weren’t any gaps when they were welded into the round tube.
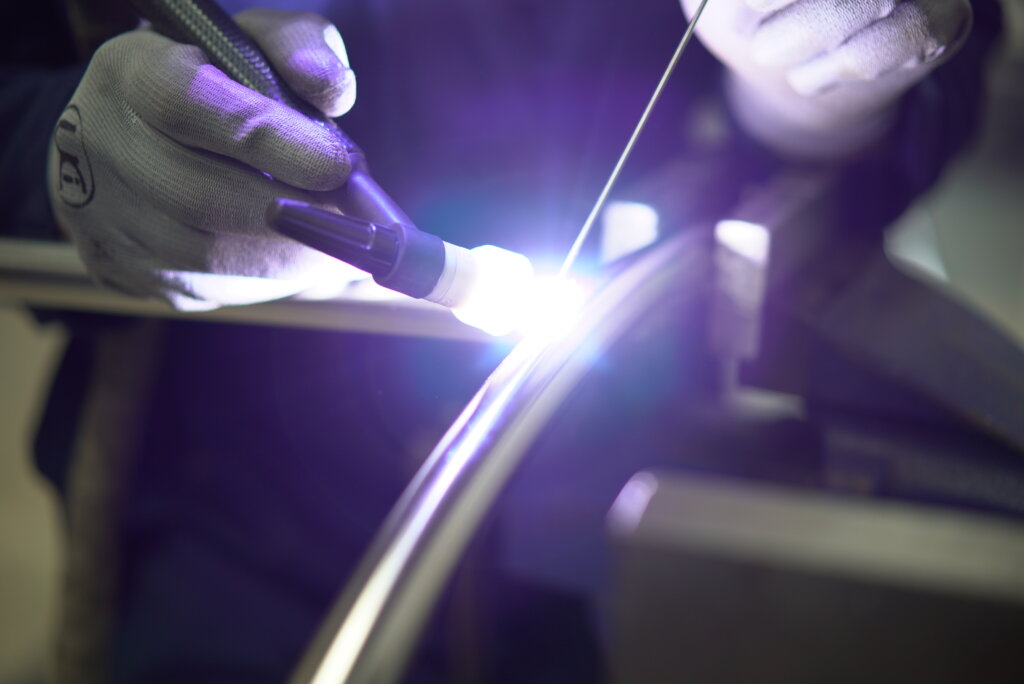
Testing the aerial apparatus
“Once the rough skeleton of the piece was made we rigged it up in the Timeless workshop and as an aerialist, I was able to assess where the hand placement would naturally fall…and that there were places for all parts of your body to have contact with. Being able to ergonomically test the piece meant that we could ensure that it would be a workable piece of apparatus.” says designer Fenella Marie.
She continues, “Throughout the making process it also became apparent that the piece would require two rigging points at the top, rather than one, to offer more stability to the structure. Tom was able to fit another one at the necessary point — it was so useful to have an engineer to make this amendment to the design. We could play about with the angle of the rigging point until it was right.”
Two 10mm-thick solid stainless steel plates drilled with carabiner-sized holes were then welded on the centre-line of the top piece of round tube. These hanging points were reinforced with extra weld to make them especially strong.
Crucially, the piece was taken to an independent weight tester once it was complete. The tester used hydraulic machinery to verify that the apparatus would have a Working Load Limit of 300kg. (The breaking strain of this 2-point hoop would exceed 300kg, but since this was a bespoke piece it was not ‘tested to destruction’!).
Tube polishing
The round tube was supplied with a mirror polish, but once all of the fabrication processes has taken place, Timeless hand-polished the moon at the Timeless polishing studio to ensure a bright finish remained in all places.
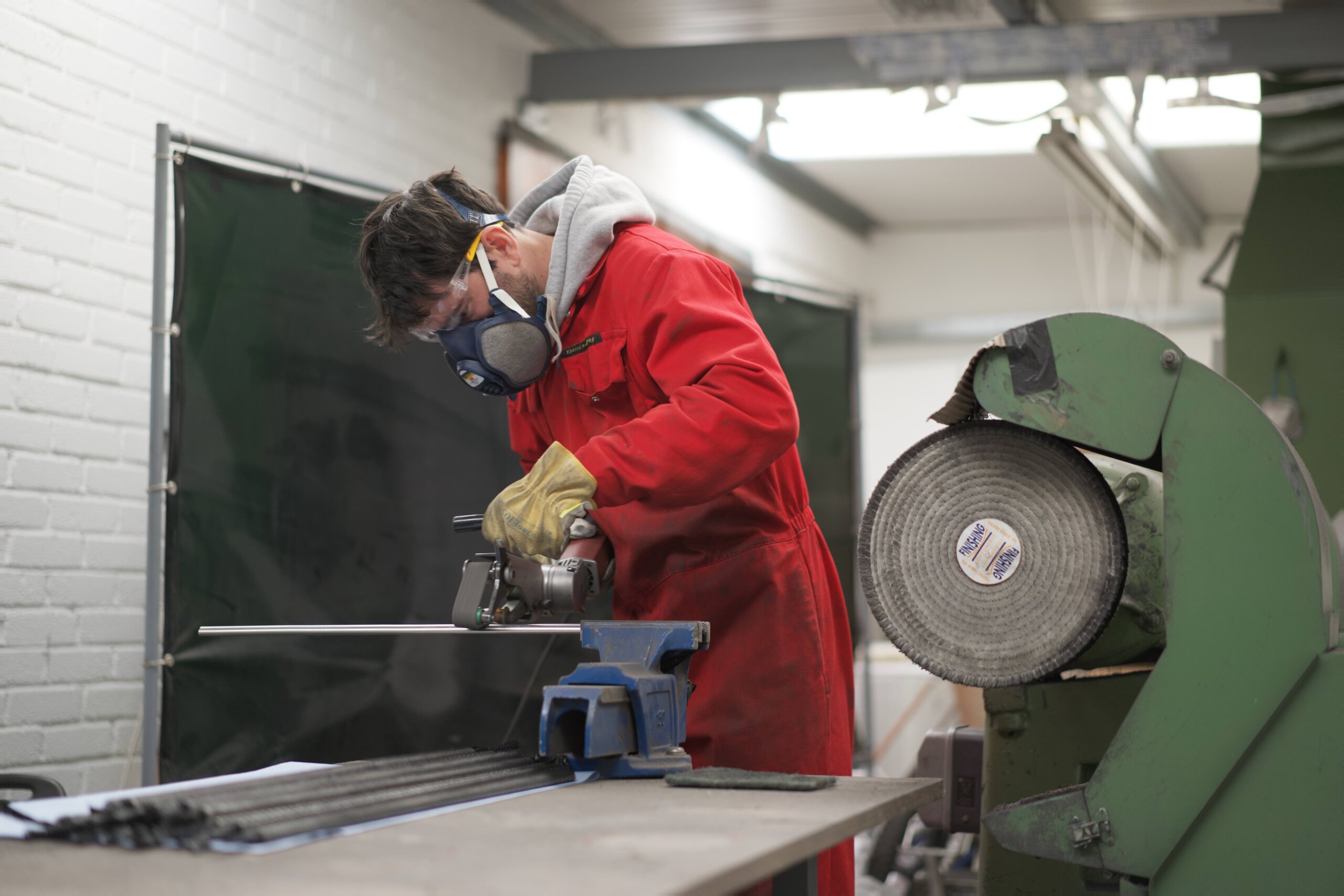
Most importantly, electrochemical cleaning was used to remove the slight discolouration that occurred around some of the welds. This passivation process helped to restore the stainless steel’s protective oxide layer, making sure that the apparatus remains resistant to corrosion.
Artistic tubing design
Timeless’s decorative tube profiles are carefully contoured to both look and feel sculptural. This has not gone unnoticed by British and international designers and artists, who regularly incorporate Timeless’s high-quality metal tubes into their designs.
“Engineering and fabricating this stunning piece proves that we are more than just steel tubing manufacturers or a metal tubing supplier. Our tubes are carefully contoured to both look and feel sculptural, so it is a joy to see them appreciated by artists in this way. We love working with artists and sculptors, and feel excited when an artistic project like this graces our workshop” says McMillan.
Find out more about our tube fabrication services.
More stories
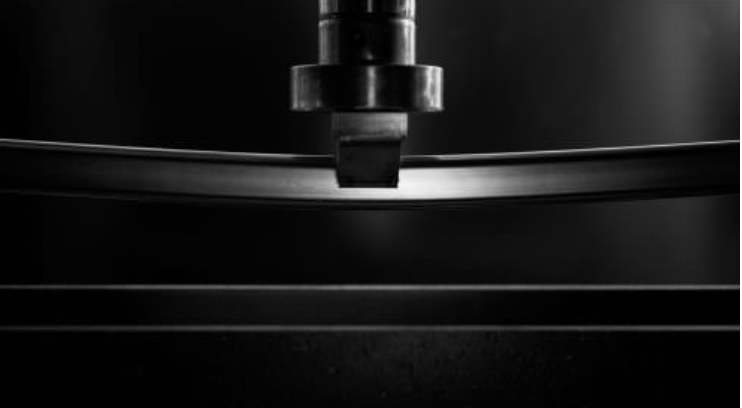
Proving the strength of formed tubes using mechanical bend tests
An exploration into two independent axial load tests on our stainless steel formed profiles, plus a brief look at how we calculate the degree of bends for formed tubes.
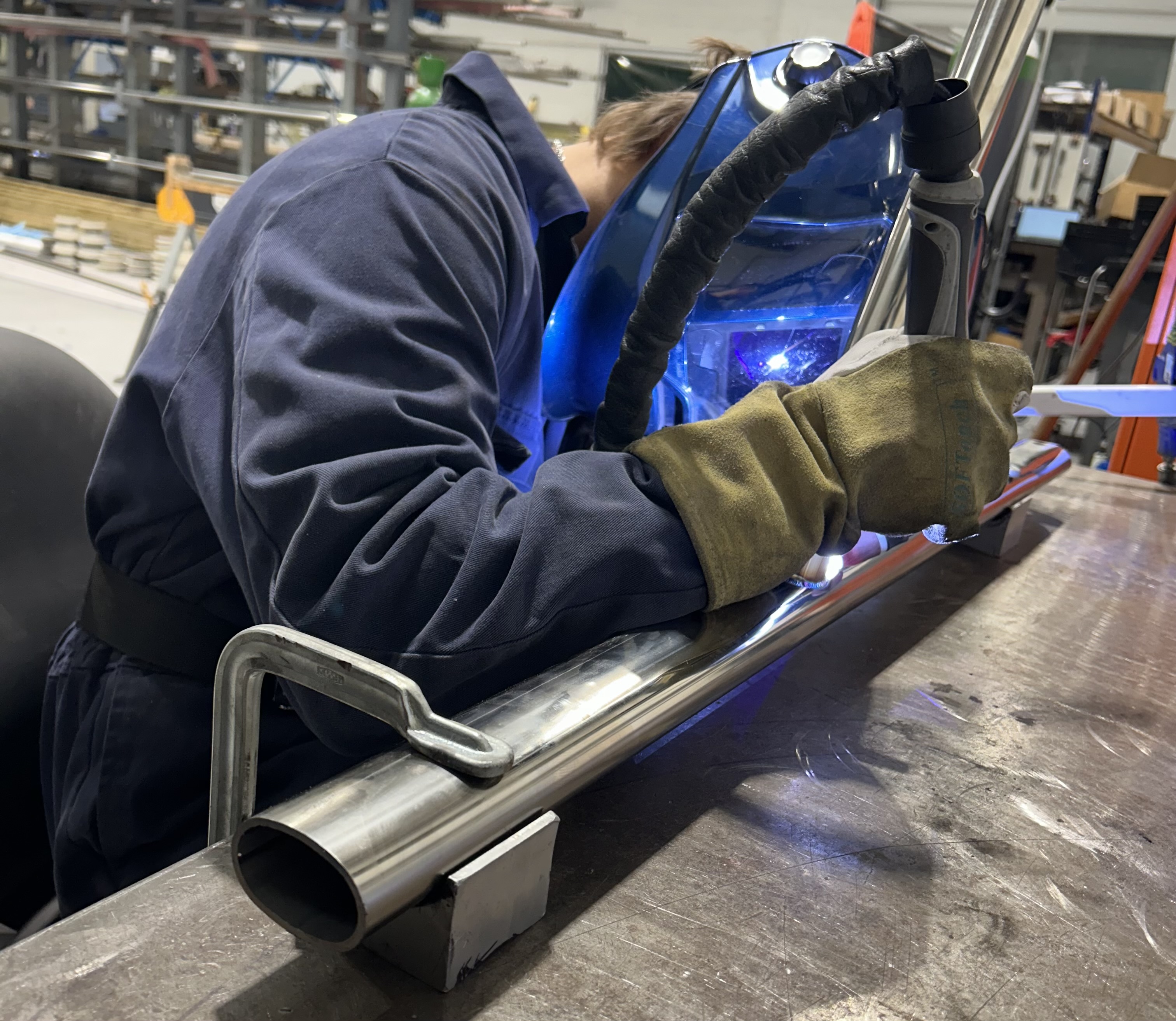
Exhibitors Timeless Tube engineer tube-based showcase for Southern Manufacturing and Electronics trade fair
Visitors to leading trade show for engineers and manufacturers to experience a showcase of innovative tube designs
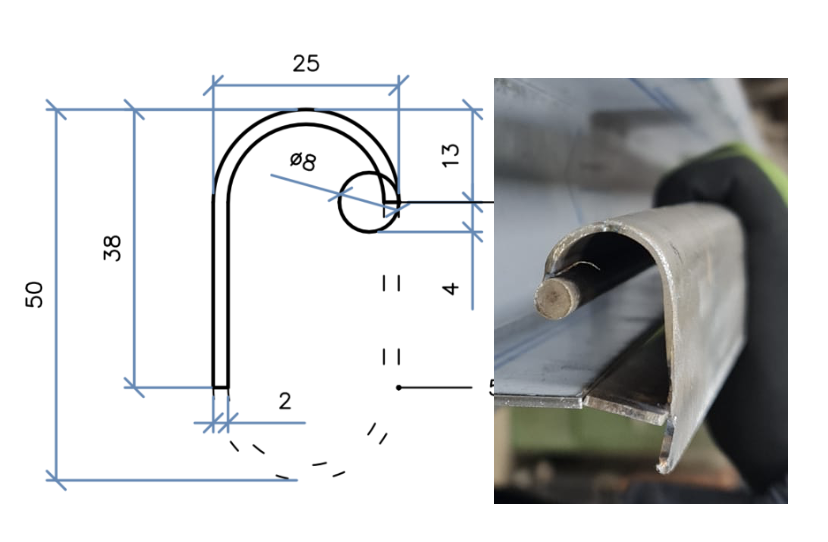
Cut Flat-sided Oval Tube Features in Stunning Recessed Handrail Project
Achieving unique designs often requires embracing trial and error. Timeless had the pleasure of working with pioneering UK-based bespoke steel fabricators Metcalfe on a one-of-a-kind recessed handrail